I posted a photo of how to install carrier bearings and thought you would like to see more QUICKSHIFT. You seem interested so here GOES IT. First off the 8.8 ford diff uses the same size carrier shims as the 12 bolt chevy. Normally i rebuild the posi units and spider gears right in the car. But its a waste of time and money. You can buy a Ford Motorsport unit for under 200 Bucks but it needs to be set up backlash wise. No two units are machined the same. So here is some photos and info. First i set the back lash to .006 on the street driven 8.8 on some rears i even go tighter and on some none at all. When selecting shims you need several sizes in duplicate thicknesses. Normally i use a solid one piece one on the ring gear side. Then i use select fit in the opposite side. The 8.8 has no provisions for spreading the case even though i have a home made spreader. So how to determine the shims. Set up the packs so the posi unit can be installed and removed with one handed hard pull. Another words select the shims for a snug to tight fit. Then add or subtract from each side equally until you get the Back lash you desire. Once this is dun remove the ring gear shim add .005 to the ring side then tap it in and you are finished. Install the caps and torque to 70 LBS. To remove the ring gear remove the bolts (The 8.8 uses right handed threads) and use a flat punch in alternating holes and tap the gear off. To install the ring gear on the new carrier use 7 Alignment pins. I normally use long bolts and cut the heads off. Then use the remaining 3 to pull the gear on the carrier. This can be dun with a long 3 inch bolts with a nut screwed all the way down to the shoulder of the bolt. Then install them in the remaining 3 holes and use the nuts to pull the gear onto the carrier. Once the gear is installed install all the stock bolts with red locktite and torque to 75 FT LBS.
I hope yo like this info you seemed to be interested in the bearing install tips i posted earlier.
Note always mark the bearing caps for direction and side. They must not be reversed. The 8.8 has an arrow that faces outward facing the wheel side. Use a punch to identify the cap location.
Specks Back lash Ford .008-.015
Ring gear torque 75 FT LBS
Carrier caps 70 Ft LBS
Pinion drag new bearings and seal installed 30-35 Inch LBS
Pinion drag no seal 25-30 INCH Lbs
Used bearings 15-20 INCH LBS seal installed
Used bearings no seal installed 10-15
AND NEVER USA A CRUSH SLEEVE. Use a solid sleeve with select shims. and loctite red on the NUT
http://i740.photobucket.com/albums/xx46/proguns/001-60.jpg
http://i740.photobucket.com/albums/xx46/proguns/002-31.jpg
http://i740.photobucket.com/albums/xx46/proguns/003-20.jpg
Tomorrow the 5 lug conversion with short Mustang axles and turbo coupe brakes and Lincoln rotors. I make custom brackets they are COOL Stay tuned for who ever is interested in this Thanks
Really. I thought a crush sleeve was universal practice for any rear end? Anywhere good I should read further on setting up rear ends? Because I obviously need some more introductory teaching. Interesting though. I will be putting a posi carrier and 3.27s in my crown vic 8.8 fairly soon so this is definitely of interest to me too. Thanks for the good post!!
Would this be the proper width for an '87-'88 Tbird/Cougar? What year(s) are you sourcing the rear axles from?Very interested in your method of this :)
First thing i must explain i use a crush sleeve eliminator. It has a spacer and selective shims. I am doing a GM 8.5 tomorrow or Monday and will take some photos. I chose the mustang 29 1/4" axles to get some tire clearance. This axle is actually mine for my Turbo Coupe. The Turbo coupe axles are 30". I removed my ABS so i do not need the tone rings. Tomorrow i am going to make the Caliper brackets. That is going to be TRICKY to say the least. But i think i have it worked out in my HEAD. I will see in the AM as they say. I will keep you posted. Thanks for asking. Axles can be researched on randys web site. ringpinion.com.
Nice write-up Tom. It's funny that you set some rear ends up with little to no back lash. Some people would shake their heads at this in amazement. WE know better don't we....LOL. When we set up the 6.00/ 9in for racing, we'd set it @ .002". Take it to the track and after a couple of 8800 RPM launches, it would end up @ .006 -.007.....just nice.
Heya Tom, not sure if you've seen it, but this thread may help ya when messing with axles, and lengths and so on.
I've got a set of rear axles from a '97 Stang (so I can keep my track width similar to my TC rear width). I just need to get some brackets, calipers, and rotors, and get crackin'.
....I think you forgot to post the link. LOL
http://www.foxtbirdcougarforums.com/showthread.php?3664-Help!-7.5-quot-Axle-to-8.8-quot-Trouble!/page6
How goes it Quick shift. Basically once you know the axle length all you do is double or if different lengths add them up. Then add in the cross shaft diameter. I use 1"as a rule so a set of TC axles of 30" would be 61" total length TO . Thanks for the link it is definitely helpful and informative. I copied it and ran a couple off on the printer for the shop. Thanks
YOU ARE SHARP THATS FOR sure THOSE zero BACK LASH SECRETS sure work. BASICALLY NOT TO MANY KNOW ABOUT THAT LITTLE TRICK. MY HATS OFF TO YOU. Sounds like you have set up some slick FINAL DRIVES. Years ago we found out about the opening up of the back lash early in my 1320 DAYS. Nice post QUICK Very NICE
OK QUICK SHIFT was messing around with the brakes on my 5 lug conversion and here is the final set UP
http://i740.photobucket.com/albums/xx46/proguns/003-21.jpg
http://i740.photobucket.com/albums/xx46/proguns/004-17.jpg
This allows me the large rotors with stock TC calipers and hardware. It also is the shortest to setup i could come up with. OTHER THAN A narrowed unit
Here is a Crush Sleeve eliminator. This is store bought. I used to make them years ago. To bad i did not PATTEN THEM. I started making them in 1964. Honest
http://i740.photobucket.com/albums/xx46/proguns/002-Copy.jpg
Nice work Tom.....love the Sawsall feller gauge...LOL. Seriously though, the idea looks good, simple and allows off the shelf parts to be used.
When we were building the race car in the 80s, coin was tight and axles were running $600 and up plus the narrowing cost, so I used a 9" from a Torino and had my Cragars modified to make a 15X12" with an 8" back space fit. It only cost $300 bucks to do the wheels!
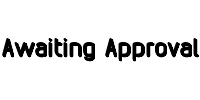
Now thats what i am talking about!!!! Nice Very nice!!!
What are the rotors from, if you don't mind my asking?
Do you plan to sell copies of the brackets/hardware what-have-you?
Rotors are LINCOLN
who is this guy??? he is giving us way tooooo much tech support!!!LOL now I am spending all my time reading your posts, good stuff!!!!
Hey, I would like some more info on the rear brake set-up, could you pm me or make a new thread:D
Well GUYS actually i like to pass on info. When i was a YOUNG people the older guys did not tell you anything about their cars. What good is knowledge if you cant pass it on. Basically i am a fabricator and an engine builder. My grandfather started the business in 1900. Then my dad then me and now JR. I love looking at mods that people do to their cars and i love passing on info. As an old guy the internet is new to me. My girls gave me this computer and i found these sites. Some of the sites banned me for telling LIES,But i did not do that. So they asked for photos so i learned how to take photos then post them. Then i was thrown off sites because they thought the photos were PHONY??? Well any way i love to mess around with my welder and make JUNK and i pass it on to everyone that will listen. Reason being i almost lost my life 2 times since i am on this planet and it scared the HELL out of me. So i post stuff that can may Be passed on after i am gone. Thanks and as soon as i complete the brakes 100% i will post more stuff Thanks
NOTE i still have to drive the car once the axle is installed in the car. Hay it might not WORK?? I have made many a part that did not work over the years. But if you do not try you never KNOW. Thanks
Thanks for the write-up, Tom. Good tips I never heard anywhere else.
I never have done a rear-end, and have a question on the crush sleeve eliminator. I would guess that you would measure the old sleeve and size the solid one to that, right? Or is there another way using a gauge to set the pinion depth?
What you do is like you said measure the original sleeve then add a few thousandths to the stack. Assemble the pinion and measure the drag. Then subtract shims by .002 until you get your drag. The drag should be about 10-15 inch pounds with old bearings and 20-25 with new ones. Remember always torque the shim stack to 100 Ft LBS for checking. Once you have your desired drag assemble the pinion with the seal installed and lock tite the nut with RED and torque it down to 125 FT LBS. This is the best way i have found to set up the PINION DRAG. I hate those Crush sleeves. Here is a home made holder. As you can see i have it drilled for just about every on the planet. Its about 4 feet long for crushing sleeves and torquing pinion nuts.
http://i740.photobucket.com/albums/xx46/proguns/005-Copy.jpg
NOTE Never tighten a crush sleeve with an impact wrench and never reuse a pinion NUT,